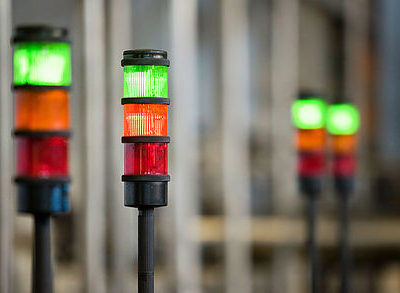
During a Kaizen event, lean tools are implemented to improve the performance of the area. A kaizen event involves not only physical changes in the area, but modifications in the way people act in the workplace. When we kaizen, we change some people’s behaviors to more productive ones. Hence the effectiveness of the improvement activity.
However, when we talk about the tools of the visual factory, this is not always the case, and the purpose of these tools has been misunderstood. Specifically if we talk about Andon, managers have an incomplete idea of the true purpose of these devices.
Andon involves the installation of devices that indicate the current status of production units (a machine, a line or an assembly cell) to easily identify when there is an abnormal situation that requires intervention and whether the actions taken were effective.
An effective Andon system must necessarily include these 4 stages:
1.Monitoring the situation
2.Communication of the abnormality to the stakeholders
3.Activity to restore normality
4. Validation of the effectiveness of the corrective action.
However, in most companies, Andon only includes the first two points and managers focus particularly on the second, on ensuring that communication is as fast as possible, but nothing more.
In the most common cases, we are talking about the installation of turrets with green and red lights whose status will indicate whether everything is in order or whether help is required.
assistance is required. In other more sophisticated cases, we see devices that send text messages or e-mails with detailed information to indicate the situation to the persons concerned.
These systems quickly degenerate into a situation where a multitude of turrets desperately clamor for attention with no one doing anything or hundreds of emails sent and ignored by the recipients. Communication happens, but it does not provoke any action. The Lean tool did not cause any productive behavior change.
Lean practitioners must be very clear that the real purpose of an Andon system is not to communicate the current situation, but to «provoke an action that restores normality». If we fail to achieve this, the Andon system is nothing more than a waste.
An effective implementation of an Andon system that addresses all 4 steps can easily be achieved by using Lean 4.0 technologies to monitor the effectiveness of each of the 4 stages.
Small micro-controllers such as Arduino or Raspberry with internet connectivity can be used to monitor the situation of the machine or production line and make a real estimate of the effectiveness of the equipment (OEE), if an abnormality is detected, the system sends notifications to the person responsible for taking action and measures the time elapsed for this person to make an appearance and the time taken to restore normality. If these times exceed the pre-established criteria, the same system escalates the situation by sending notifications to the management group and measuring the time elapsed for them to take action. Additionally, if once normality is restored, the system detects again the need for attention, we can assume that the previous actions were not effective and escalate again to require management participation.
Let’s remember an important premise: If we measure it, we can improve it, and with the above strategy, all this activity of alarms generated, times recorded and actions taken and their effectiveness is recorded in a database that we can analyze to manage performance and continue modifying behavior patterns, that is, to continue doing Kaizen.
If you would like to receive information on how to make an effective implementation of ANDON under a Lean 4.0 initiative with iGo&See please send me a message or comment below and I will gladly give you all the information.